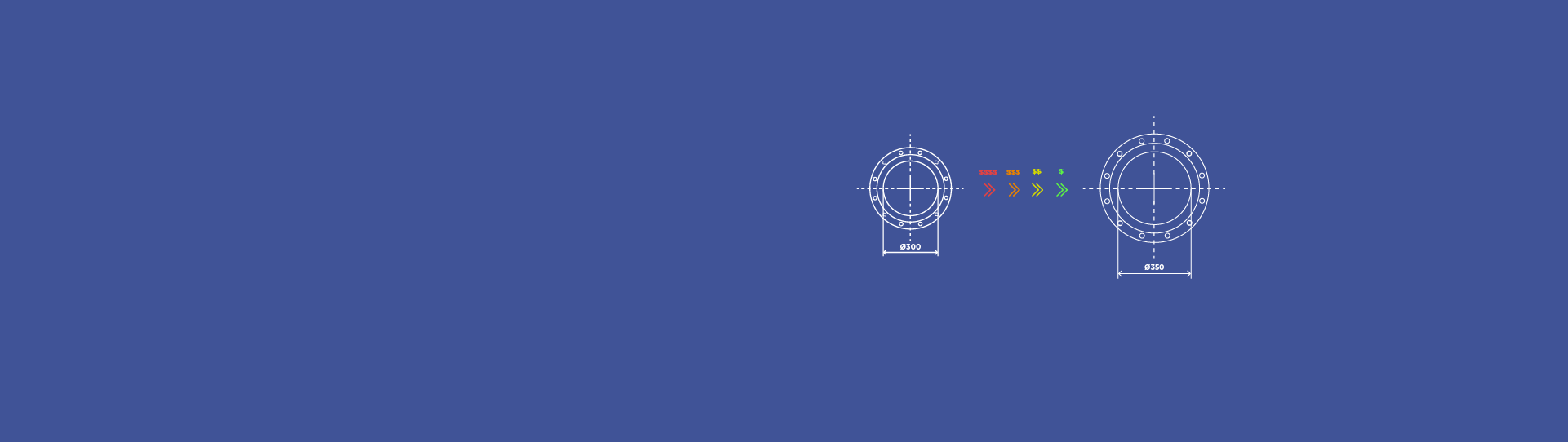
How selecting a pump with a larger discharge flange cuts your operating costs
Imagine cutting your energy costs by simply upgrading the size of your pump's discharge flange. It’s not just a technical tweak; it’s a smarter, more sustainable way to protect your bottom line. With a small change, you can make a big impact on your profitability and the future of your operations.
- 40 m SDR17 Ø315 PE pipe (Ø278 mm internal diameter) for DN300 discharge flange
- 4 x 90° bends
- Flow (Q) = 920 m3/h
- Static head = 6 m
- Dynamic head 3,4 m (pipe friction)
- Total head = 9,4 mLC
- 40 m SDR17 Ø400 PE (Ø353 internal diameter) pipe for DN350 discharge flange
- 4 x 90° bends
- Flow (Q) = 920 m3/h
- Static head = 6 m
- Dynamic head 1,19 m (pipe friction)
- Total head = 7,19 mLC
A reduction of 2,21 mLC is achieved by enlarging the discharge pipe.
And this reduced head can be converted into power (given as P2) with a simple formula:
A saving of 6,84 kWh between setup 1 and setup 2 (29,1 kW minus 22,26 kW)
If we imagine that there are 32 pumps each running 24/7/365 (which is 8760 hours) then this 6,84 kWh reduction in power adds up to 1.917.802 kWh every year and with the cost of energy today then this amounts to a massive saving in energy costs, which in turn leads to greater profitability in your business.
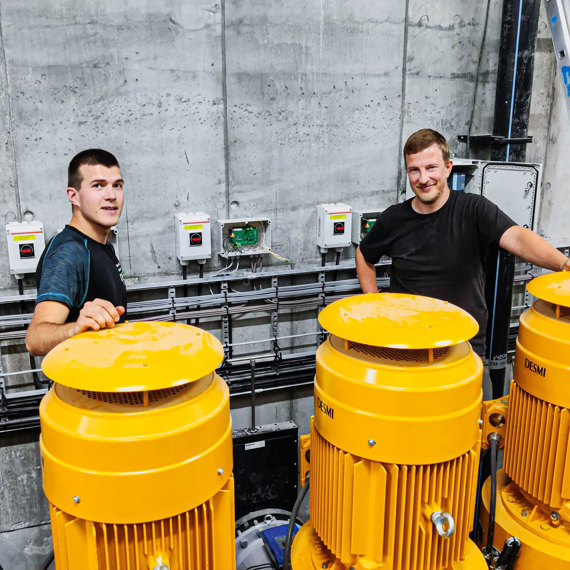
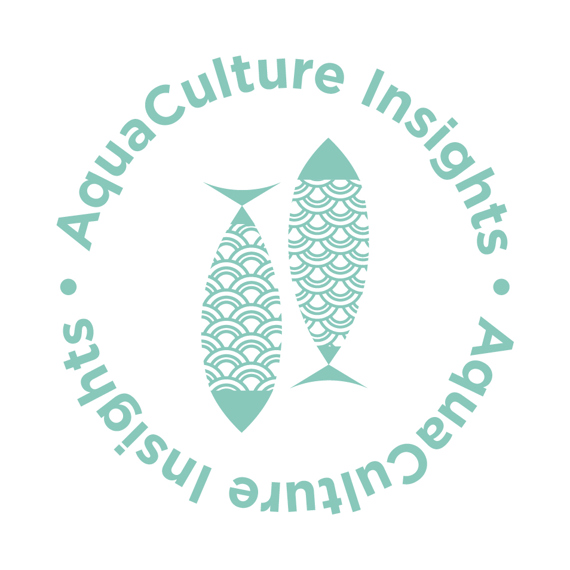