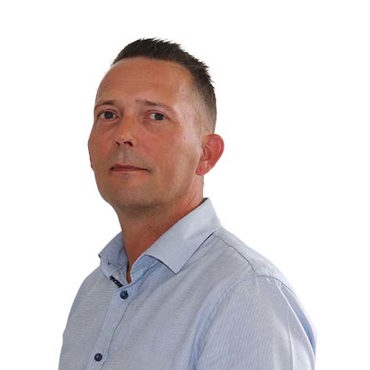
Johan Schwerin
Managing Director - DESMI DeServe A/S
October 2018
Developing and supplying reliable pumps is only part of the equation for DESMI. State-of-the art field service gives customers peace of mind, wherever their pumps are installed and whatever the configuration.
Full-service options
DESMI supports pump systems installed at everything from district heating plants to battleships. Differing types of service are available for differing client needs and the deep know-how of the field engineers allows them to maintain competitor brands, too.
If a pump breaks down, the Fix on Failure solution brings in field engineers to overhaul the system and determine if the issue is due to wear or an installation problem.
For a more proactive approach, DESMI offers preventative maintenance contracts. These define service intervals to verify that everything is running properly and assess the risk of failure within the next contract period.
The condition-based service approach takes proactivity even further, with engineers coming in at shorter intervals and ensuring every time that overall performance is as efficient as possible. These regular visits let DESMI’s engineers monitor the pumps and also check that bearings and other potentially worn parts are operating as expected. Such check-ups ensure that pumps operate at their highest efficiency – and can result in big savings.
Service that pays its way
Just how much money can be saved? According to Johan Schwerin, DESMI’s Service Manager, “Restoring a loss of perhaps 5 percent in efficiency (with a 55kw motor or larger) can easily pay the cost of a service visit in sheer energy savings.”
DESMI field engineers are usually able to deliver savings on their first site visit - often through some fairly simple adjustments to correct the pump farm not running as efficiently as possible. In fact, the company offers an initial service visit for free because long experience shows that there is almost always potential for optimisation. And there’s often no charge for the first service visit if no improvements can be identified.
“We experience more and more often that if there’s a problem with the customer’s installation, it’s not the pump that is at fault,” explains Johan Schwerin. “Instead, the installation may be poorly suited to the pump (or vice versa), or the pump may have been incorrectly installed. Usually, a visit from a service technician can take care of such problems.”
Expertise in action
In a recent case, DESMI received an urgent call for help from a shipbuilding client who had run into a problem installing a number of the vessel’s pumps. The motors on four NSLH (horizontally mounted) pumps needed to be turned 45 degrees to suit the installation. And the deadline? ASAP, of course.
Within three hours of the client’s call, a service technician from Denmark was on site – and he was joined shortly after by a DESMI colleague from Germany. By the time the DESMI technicians left the site at 10 pm that evening, the work for all the pumps had been completed and the client was able to install the system as planned.
Done right – right from the start
When installing and commissioning a pump or pump system, it’s worth getting a DESMI field engineer on site to help ensure the installation is correct and that the pump gets a good start. Confirming that a pump system works at its best duty point from the outset maximizes results and means it’s likely to last longer, too. It is particularly important to ensure a correct start for pumps and pump systems to avoid damaging dry runs – especially as the seals are likely to sustain damage from an incorrect start-up.
DESMI also performs installation and commissioning for automation, which encompasses frequency inverter filters, complete solutions for control panels, Human Machine Interfaces (HMI) and more. Confirming that the leading current coming from the frequency inverter won’t damage the pump is the first part of an automation project check. From there, DESMI technicians work their way through the entire installation to identify potential performance issues related to piping or other parameters.
Finding solutions beyond the pump
When performing installation checks or conducting service calls, DESMI’s engineers don’t just examine the pump. They take the widest possible view of the pumping system and its surroundings, allowing them to consider every possibility and address the root cause. Could the problem be the pump’s bearings? Or might it be related to the surroundings? Is a different fly wheel required, perhaps? Is head/inlet pressure as expected?
With both preventative and condition-based service, sophisticated vibration analysis helps DESMI technicians discover the truth. So, too, does looking at the factors around or inside the pump. In the end, being able to accurate determine what’s wrong, be it the pump, the piping before or after, or something else entirely, allows DESMI’s field engineers to come up with a solution or adjust the pump’s performance to suit the unique situation and perform to expectations.
A complete overview
DESMI’s trained technicians are backed by a sophisticated system that registers all customer equipment – both DESMI-branded and competitor brands – and plans service visits and technical resources. The system decreases the potential for costly repair delays as technicians know if any parts have been installed that differ from the pump’s original specifications and can ensure they bring all necessary parts. It also registers software versions, where relevant, and gives technicians access to all available data about the pumping system and its previous service history.
After every service, DESMI’s technicians produce a full report on the condition of the installation and any repairs that may soon be needed. And anything that can immediately be done to increase pump efficiency is also communicated.
Value-add
When a customer purchases a service package either from DESMI or from a competitor, DESMI may offer to hold critical spares in stock. Having these parts on hand at DESMI enables customers to minimise costly downtime by reducing repair time by as much as several weeks.
As part of any pump package, DESMI can also offer training in simple maintenance, enabling in-house crew to help keep the pump system running smoothly and efficiently.
Faster and more remote
What does the future hold for DESMI’s pump and automation field services? A key direction for the company is condition monitoring via remote surveillance. To do it, DESMI’s R&D department is exploring an Internet of Things (IOT) approach that permits better monitoring of pump state and efficiency – and enables a service technician to be deployed at the optimal moment.
Today, already, customers can choose to set up remote access to their pump systems, enabling them or DESMI’s own service engineers to monitor for faults and breakdowns from other locations. This capability is becoming more and more popular as pump installations grow in size and complexity – and when customers get a glimpse of the savings achievable in this way.
Managing Director - DESMI DeServe A/S
February 2025
January 2025
October 2024
September 2024