
Huntsman looking for a better solution
Magnetically coupled pump reduces maintenance costs.
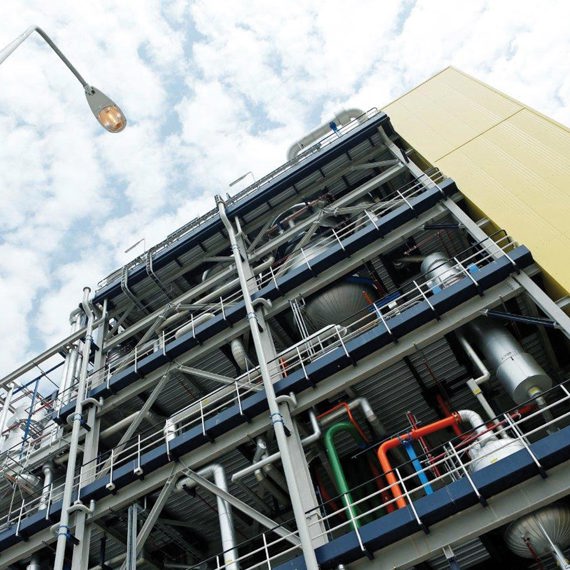
HARDENING AND HIGH MAINTENANCE COSTS
Huntsman Holland is one of the chemical companies that pay great attention to the protection of employees and preserving the environment. This major chemical chain started in the 60s as ICI in the Botlek area and now produces with five facilities, spread over an area of 180 hectares, raw materials for the polyurethanes industry. In this production process, substances such as sorbitol, amines and sucrose are used to make polyols. MDI is made with another process. They are all products and semi-finished products which are used in the insulation market, the automotive industry, the adhesive industry and as raw material for footwear, furniture, and a wide variety of plastics.
LARGE NUMBER OF PUMPS
Within the five facilities there are many pumps for the transport of the various raw materials. Previously pumps with mechanical seals were used, but which in practice were problematic, says Mechanical Maintenance Engineer, René van de Vlugt. “In this case, when these pumps exhibit leakage, it is not a particularly big problem for the environment and man. The spilled material hardens immediately when it comes in contact with the atmosphere, especially if it is wet, and will not spread in the area. However, this hardening creates relatively much work for the maintenance department. The material must literally be chipped away and then the pump and the surroundings must be cleaned. Then, of course, the leak must be fixed. In short: the maintenance costs of these pumps were (too) high. For this reason it was decided to employ a ‘zero-drip’ policy, in which we don’t tolerate any leakage.”
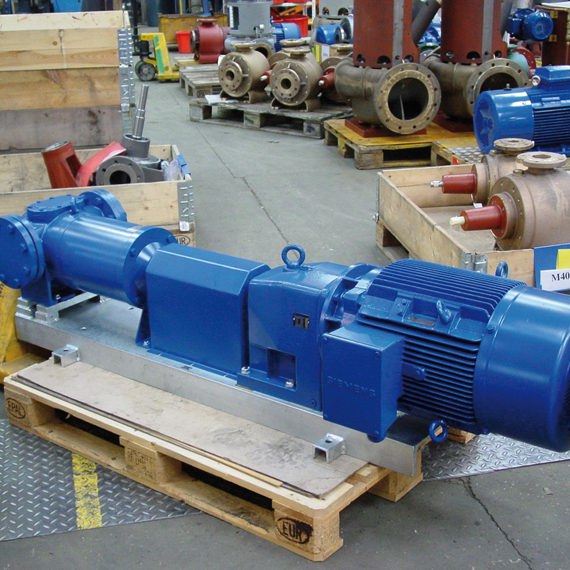
MONO-BLOCK UNIT
Other positive characteristics lie in the fact that liquid to be treated is handled relatively carefully in this pump, the high suction vacuum, and the possibility for pumping high-viscosity fluids. The ROTAN® ED pump is designed as a mono-block unit, meaning that it is directly linked to an IEC motor, gear motor or gearbox with IEC motor. Alternatively, a pump with a free shaft end is assembled with a drive via a flexible coupling. When the application requires the presence or removal of heat it is also possible to provision the pump head and magnets with an external casing.
LOWER MAINTENANCE COSTS
“The reason we contacted DESMI was that we already had a number of ROTAN® pumps and we were generally satisfied with them.” said Van der Vlugt. “In fact, the first pumps which we purchased in 2004, still operate without problems. Based on this experience, it was decided to to replace all pumps in the process concerned with a mechanical seal by a magnetically coupled construction. Our policy with respect to maintenance and procurement of materials is simply clear: we go for the best materials to minimise maintenance costs and maximize process reliability. That does mean that the investments are higher, but these higher costs certainly weigh up against the maintenance costs which you incur, or in the worst case, disruption or downtime of your process due to spills arising from the use of pumps with a mechanical seal.” The replacement of existing pumps is in full swing and it is a continuous process that will take a number of years. When constructing new installations magnetically coupled pumps are included as standard in the specification.